Continuously Variable Neutral Density Filter Wheel for 30 mm Cage System
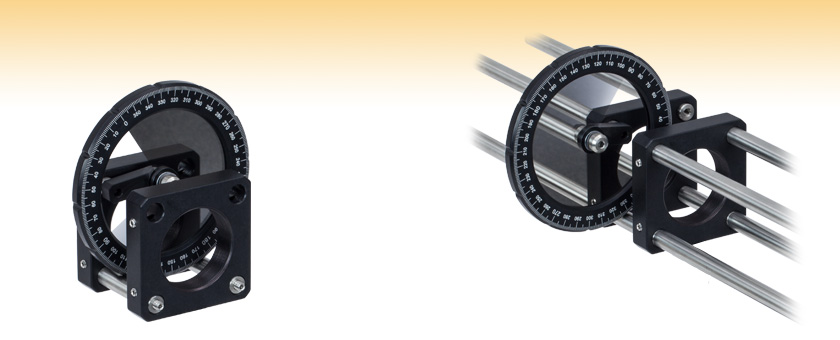
- Continuously Variable Neutral Density Filter Wheel
- SM1 Lens Tube and 30 mm Cage System Compatible
NDM2
Wheel Rotates Into
and Out of Beam Path

Please Wait
Variable ND Selection Guide | ||||||
---|---|---|---|---|---|---|
Image | ![]() |
![]() |
![]() |
![]() |
![]() |
![]() |
ND Filter Type |
Round Step | Round Continuous |
Cage Compatible |
Rectangular Step |
Rectangular Continuous |
Variable Absorptive ND Filter |
Features
- Circular, Continuously Variable, Reflective Neutral Density Filter
- Optical Density Range: 0 - 2.0 or 0 - 4.0
- Ø50 mm Filter Wheel
- Designed for Use with SM1 Lens Tubes and 30 mm Cage Systems
These circular, 30 mm cage plate-mounted, continuously variable reflective neutral density filters provide linear, adjustable attenuation within the coated region via rotation. They are specifically designed for compatibility with our SM1 Lens Tubes and 30 mm Cage System. They are composed of a UV fused silica glass substrate and a metallic Inconel coating through a full 270°, ensuring a flat spectral response from the ultraviolet to the mid-infrared. These filters have optical densities ranging from either 0 to 2.0 or 0 to 4.0. For the variation of optical density with angle, please refer to the Specs tab.
The circular filter wheel measures 50 mm in diameter and is attached to a rotating lever arm so that it can be moved out of the beam path. The rotating axle comes with angular graduations that improve repeatability. In addition, an 8-32 (M4) tapped hole is provided in the base to allow for mounting to our Ø1/2" posts and accessories. The plates on either side of the filter wheel contain an internally threaded SM1 port and have four through holes that allow mounting to our ER cage system assembly rods.
Optical density (OD) indicates the attenuation factor provided by an optical filter, i.e. how much it reduces the optical power of an incident beam. OD is related to the transmission, T, by the equation
where T is a value between 0 and 1. Choosing an ND filter with a higher optical density will translate to lower transmission and greater reflection of the incident light. For higher transmission and less reflection, a lower optical density would be appropriate. As an example, if a filter with an OD of 2 results in a transmission value of 0.01, this means the filter attenuates the beam to 1% of the incident power. Please note that it is typical to see as much as a 50% drop in power going from the uncoated region to the coated region for filters with a max OD of 4.
The Inconel coating on these filters is a very hard metallic alloy that is resistant to aging under normal conditions, but will oxidize at elevated temperatures. It is therefore recommended that the neutral density filters be used at temperatures below 100° C.
These filters are not intended to serve as laser safety equipment. For lab safety, Thorlabs offers an extensive line of safety and blackout products that significantly reduces exposure to stray or reflected light.
General Specifications | |
---|---|
Substrate Material | UV Fused Silicaa |
Diameter Tolerance (A & B) | Outer Diameter: +0.00/-0.25 mm Inner Diameter:+0.25/- 0.00 mm |
Thickness Tolerance (C & D) | ±0.25 mm |
Coating Radial Angle (E) | ±1o |
Spectral Range | 240 - 1200 nm |
Coating | Front: Inconel (NiCrFe) Back: Uncoated |
Irregularity (per cm2) | <λ |
Surface Quality | 60-40 Scratch-Dig |
Wedge | <3 arcmin |
Optical Density Tolerance | ±5% (At Both Extremes) |
Round Continuously Variable Metallic ND Filters (Unmounted Dimensions) | |||||||
---|---|---|---|---|---|---|---|
Item # | Optical Density (OD) | A | B | C | D | E | F |
NDM2 | 0 - 2.0 | 50 mm | 7.5 mm | 8 mm | 48 mm | 270o | 2 mm |
NDM4 | 0 - 4.0 | 50 mm | 7.5 mm | 8 mm | 48 mm | 270o | 2 mm |
Optical Density as a Function of Angle
The optical density is a linear function of the angle:
OD = mθ
where OD is the optical density and θ is the angle in degrees. The value of m depends upon the optical density range of the particular ND filter:
- For filters with an OD range of 0 - 2.0, m = 0.00741.
- For filters with an OD range of 0 - 4.0, m = 0.0148.
This formula assumes 0° at the point where the coating begins and 270º at the end of the coating (i.e., the point of highest optical density).
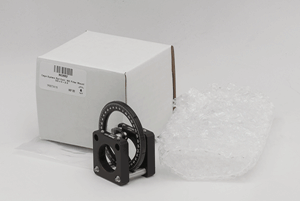
Click to Enlarge
Figure 3.2 NDM2 Packaging
Table 3.1 Specifications | ||
---|---|---|
Item # | % Weight Reduction |
CO2-Equivalent Reductiona |
NDM2 | 58.64% | 2.08 kg |
NDM2/M | 58.64% | 3.07 kg |
NDM4 | 58.64% | 6.13 kg |
NDM4/M | 58.64% | 4.50 kg |
Smart Pack
- Reduce Weight of Packaging Materials
- Increase Usage of Recyclable Packing Materials
- Improve Packing Integrity
- Decrease Shipping Costs
Thorlabs' Smart Pack Initiative is aimed at waste minimization while still maintaining adequate protection for our products. By eliminating any unnecessary packaging, implementing packaging design changes, and utilizing eco-friendly packaging materials for our customers when possible, this initiative seeks to improve the environmental impact of our product packaging. Products listed in Table 3.1 are now shipped in re-engineered packaging that minimizes the weight and the use of non-recyclable materials.b As we move through our product line, we will indicate re-engineered packages with our Smart Pack logo.
Cage System Overview
The Cage Assembly System provides a convenient way to construct large optomechanical systems with an established line of precision-machined building blocks designed for high flexibility and accurate alignment.
16 mm, 30 mm, and 60 mm Cage System Standards
Thorlabs offers three standards defined by the center-to-center spacing of the cage assembly rods (see Figure 14A). The 16 mm cage, 30 mm cage, and 60 mm cage standards are designed to accommodate Ø1/2", Ø1", and Ø2" optics, respectively. Specialized cage plates that allow smaller optics to be directly inserted into our larger cage systems are also available.
Standard Threads
The flexibility of our Cage Assembly System stems from well-defined mounting and thread standards designed to directly interface with a wide range of specialized products. The three most prevalent thread standards are our SM05 Series (0.535"-40 thread), SM1 Series (1.035"-40 thread), and SM2 Series (2.035"-40 thread), all of which were defined to house the industry's most common optic sizes. Essential building blocks, such as our popular lens tubes, directly interface to these standards.

Figure 14A An example of the standard cage plate measurements determining cage system compatibility.
Standard Cage System Measurements | |||
---|---|---|---|
Cage System | 16 mm | 30 mm | 60 mm |
Thread Series | SM05 | SM1 | SM2 |
Rod to Rod Spacing | 16 mm (0.63") | 30 mm (1.18") | 60 mm (2.36") |
Total Length | 25 mm (0.98") | 41 mm (1.60") | 71.1 mm (2.80") |
Cage Components | ||
---|---|---|
Cage Rods | 16 mm | These rods are used to connect cage plates, optic mounts, and other components in the cage system. The SR Series Cage Rods are compatible with our 16 mm cage systems, while the 30 mm and 60 mm cage systems use ER Series Cage Rods. |
30 mm | ||
60 mm | ||
Cage Plates | 16 mm | These serve as the basic building blocks for a cage system. They may have SM-threaded central bores, smooth bores sized for industry standard optics or to accommodate the outer profile of our SM Series Lens Tubes, or specialized bores for other components such as our FiberPorts. |
30 mm | ||
60 mm | ||
Optic Mounts | 16 mm | Thorlabs offers fixed, kinematic, rotation, and translation mounts specifically designed for our Cage Systems. |
30 mm | ||
60 mm | ||
Cage Cubes | 16 mm | These cubes are useful for housing larger optical components, such as prisms or mirrors, or optics that need to sit at an angle to the beam path, such as beamsplitters. Our cage cubes are available empty or with pre-mounted optics. |
30 mm | ||
60 mm | ||
Replacement Setscrews | Replacement setscrews are offered for our 16 mm (SS4B013, SS4B025, and SS4B038) and 30 mm (SS4MS5 and SS4MS4) cage systems products. | |
Post and Breadboard Mounts and Adapters | Mounting options for cage systems can be found on our Cage System Construction pages. Cage Systems can be mounted either parallel or perpendicular to the table surface. | |
Size Adapters | Cage System Size Adapters can be used to integrate components from different cage system and threading standards. | |
Specialized Components | Thorlabs also produces specialized cage components, such as Filter Wheels, a HeNe Laser Mount, and a FiberPort Cage Plate Adapter, allowing a wide range of our products to be integrated into cage-mounted optical systems. Explore our Cage Systems Visual Navigation Guide to see the full range of Thorlabs' cage components. |
Table 5.1 Damage Threshold Specifications | |
---|---|
Optical Density | Damage Threshold |
0.3 | 0.025 J/cm2 (355 nm, 10 ns, 10 Hz, Ø0.772 mm) |
1.0 | 0.05 J/cm2 (355 nm, 10 ns, 10 Hz, Ø0.772 mm) |
2.0 | 0.075 J/cm2 (355 nm, 10 ns, 10 Hz, Ø0.772 mm) |
Damage Threshold Data for Thorlabs' Continuously Variable Metallic ND Filters
The specifications in Table 5.1 are measured damage thresholds for our non-variable ND filters. Our continuously variable metallic ND filters will exhibit similar performance at the discrete values listed. Damage threshold specifications are constant for a given optical density, regardless of the size of the filter.
Laser Induced Damage Threshold Tutorial
The following is a general overview of how laser induced damage thresholds are measured and how the values may be utilized in determining the appropriateness of an optic for a given application. When choosing optics, it is important to understand the Laser Induced Damage Threshold (LIDT) of the optics being used. The LIDT for an optic greatly depends on the type of laser you are using. Continuous wave (CW) lasers typically cause damage from thermal effects (absorption either in the coating or in the substrate). Pulsed lasers, on the other hand, often strip electrons from the lattice structure of an optic before causing thermal damage. Note that the guideline presented here assumes room temperature operation and optics in new condition (i.e., within scratch-dig spec, surface free of contamination, etc.). Because dust or other particles on the surface of an optic can cause damage at lower thresholds, we recommend keeping surfaces clean and free of debris. For more information on cleaning optics, please see our Optics Cleaning tutorial.
Testing Method
Thorlabs' LIDT testing is done in compliance with ISO/DIS 11254 and ISO 21254 specifications.
First, a low-power/energy beam is directed to the optic under test. The optic is exposed in 10 locations to this laser beam for 30 seconds (CW) or for a number of pulses (pulse repetition frequency specified). After exposure, the optic is examined by a microscope (~100X magnification) for any visible damage. The number of locations that are damaged at a particular power/energy level is recorded. Next, the power/energy is either increased or decreased and the optic is exposed at 10 new locations. This process is repeated until damage is observed. The damage threshold is then assigned to be the highest power/energy that the optic can withstand without causing damage. A histogram such as that below represents the testing of one BB1-E02 mirror.
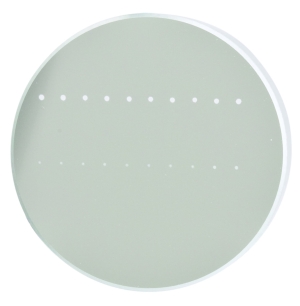
The photograph above is a protected aluminum-coated mirror after LIDT testing. In this particular test, it handled 0.43 J/cm2 (1064 nm, 10 ns pulse, 10 Hz, Ø1.000 mm) before damage.
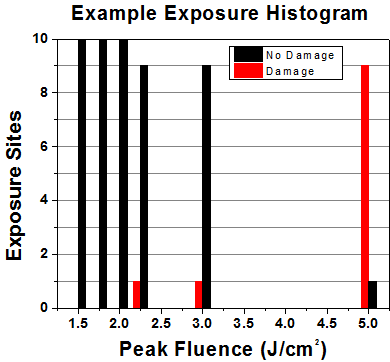
Example Test Data | |||
---|---|---|---|
Fluence | # of Tested Locations | Locations with Damage | Locations Without Damage |
1.50 J/cm2 | 10 | 0 | 10 |
1.75 J/cm2 | 10 | 0 | 10 |
2.00 J/cm2 | 10 | 0 | 10 |
2.25 J/cm2 | 10 | 1 | 9 |
3.00 J/cm2 | 10 | 1 | 9 |
5.00 J/cm2 | 10 | 9 | 1 |
According to the test, the damage threshold of the mirror was 2.00 J/cm2 (532 nm, 10 ns pulse, 10 Hz, Ø0.803 mm). Please keep in mind that these tests are performed on clean optics, as dirt and contamination can significantly lower the damage threshold of a component. While the test results are only representative of one coating run, Thorlabs specifies damage threshold values that account for coating variances.
Continuous Wave and Long-Pulse Lasers
When an optic is damaged by a continuous wave (CW) laser, it is usually due to the melting of the surface as a result of absorbing the laser's energy or damage to the optical coating (antireflection) [1]. Pulsed lasers with pulse lengths longer than 1 µs can be treated as CW lasers for LIDT discussions.
When pulse lengths are between 1 ns and 1 µs, laser-induced damage can occur either because of absorption or a dielectric breakdown (therefore, a user must check both CW and pulsed LIDT). Absorption is either due to an intrinsic property of the optic or due to surface irregularities; thus LIDT values are only valid for optics meeting or exceeding the surface quality specifications given by a manufacturer. While many optics can handle high power CW lasers, cemented (e.g., achromatic doublets) or highly absorptive (e.g., ND filters) optics tend to have lower CW damage thresholds. These lower thresholds are due to absorption or scattering in the cement or metal coating.
LIDT in linear power density vs. pulse length and spot size. For long pulses to CW, linear power density becomes a constant with spot size. This graph was obtained from [1].
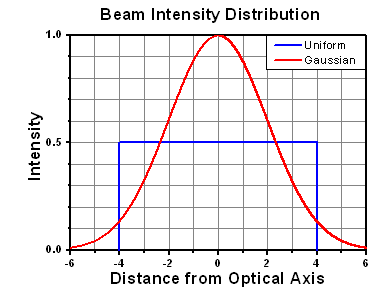
Pulsed lasers with high pulse repetition frequencies (PRF) may behave similarly to CW beams. Unfortunately, this is highly dependent on factors such as absorption and thermal diffusivity, so there is no reliable method for determining when a high PRF laser will damage an optic due to thermal effects. For beams with a high PRF both the average and peak powers must be compared to the equivalent CW power. Additionally, for highly transparent materials, there is little to no drop in the LIDT with increasing PRF.
In order to use the specified CW damage threshold of an optic, it is necessary to know the following:
- Wavelength of your laser
- Beam diameter of your beam (1/e2)
- Approximate intensity profile of your beam (e.g., Gaussian)
- Linear power density of your beam (total power divided by 1/e2 beam diameter)
Thorlabs expresses LIDT for CW lasers as a linear power density measured in W/cm. In this regime, the LIDT given as a linear power density can be applied to any beam diameter; one does not need to compute an adjusted LIDT to adjust for changes in spot size, as demonstrated by the graph to the right. Average linear power density can be calculated using the equation below.
The calculation above assumes a uniform beam intensity profile. You must now consider hotspots in the beam or other non-uniform intensity profiles and roughly calculate a maximum power density. For reference, a Gaussian beam typically has a maximum power density that is twice that of the uniform beam (see lower right).
Now compare the maximum power density to that which is specified as the LIDT for the optic. If the optic was tested at a wavelength other than your operating wavelength, the damage threshold must be scaled appropriately. A good rule of thumb is that the damage threshold has a linear relationship with wavelength such that as you move to shorter wavelengths, the damage threshold decreases (i.e., a LIDT of 10 W/cm at 1310 nm scales to 5 W/cm at 655 nm):
While this rule of thumb provides a general trend, it is not a quantitative analysis of LIDT vs wavelength. In CW applications, for instance, damage scales more strongly with absorption in the coating and substrate, which does not necessarily scale well with wavelength. While the above procedure provides a good rule of thumb for LIDT values, please contact Tech Support if your wavelength is different from the specified LIDT wavelength. If your power density is less than the adjusted LIDT of the optic, then the optic should work for your application.
Please note that we have a buffer built in between the specified damage thresholds online and the tests which we have done, which accommodates variation between batches. Upon request, we can provide individual test information and a testing certificate. The damage analysis will be carried out on a similar optic (customer's optic will not be damaged). Testing may result in additional costs or lead times. Contact Tech Support for more information.
Pulsed Lasers
As previously stated, pulsed lasers typically induce a different type of damage to the optic than CW lasers. Pulsed lasers often do not heat the optic enough to damage it; instead, pulsed lasers produce strong electric fields capable of inducing dielectric breakdown in the material. Unfortunately, it can be very difficult to compare the LIDT specification of an optic to your laser. There are multiple regimes in which a pulsed laser can damage an optic and this is based on the laser's pulse length. The highlighted columns in the table below outline the relevant pulse lengths for our specified LIDT values.
Pulses shorter than 10-9 s cannot be compared to our specified LIDT values with much reliability. In this ultra-short-pulse regime various mechanics, such as multiphoton-avalanche ionization, take over as the predominate damage mechanism [2]. In contrast, pulses between 10-7 s and 10-4 s may cause damage to an optic either because of dielectric breakdown or thermal effects. This means that both CW and pulsed damage thresholds must be compared to the laser beam to determine whether the optic is suitable for your application.
Pulse Duration | t < 10-9 s | 10-9 < t < 10-7 s | 10-7 < t < 10-4 s | t > 10-4 s |
---|---|---|---|---|
Damage Mechanism | Avalanche Ionization | Dielectric Breakdown | Dielectric Breakdown or Thermal | Thermal |
Relevant Damage Specification | No Comparison (See Above) | Pulsed | Pulsed and CW | CW |
When comparing an LIDT specified for a pulsed laser to your laser, it is essential to know the following:
LIDT in energy density vs. pulse length and spot size. For short pulses, energy density becomes a constant with spot size. This graph was obtained from [1].
- Wavelength of your laser
- Energy density of your beam (total energy divided by 1/e2 area)
- Pulse length of your laser
- Pulse repetition frequency (prf) of your laser
- Beam diameter of your laser (1/e2 )
- Approximate intensity profile of your beam (e.g., Gaussian)
The energy density of your beam should be calculated in terms of J/cm2. The graph to the right shows why expressing the LIDT as an energy density provides the best metric for short pulse sources. In this regime, the LIDT given as an energy density can be applied to any beam diameter; one does not need to compute an adjusted LIDT to adjust for changes in spot size. This calculation assumes a uniform beam intensity profile. You must now adjust this energy density to account for hotspots or other nonuniform intensity profiles and roughly calculate a maximum energy density. For reference a Gaussian beam typically has a maximum energy density that is twice that of the 1/e2 beam.
Now compare the maximum energy density to that which is specified as the LIDT for the optic. If the optic was tested at a wavelength other than your operating wavelength, the damage threshold must be scaled appropriately [3]. A good rule of thumb is that the damage threshold has an inverse square root relationship with wavelength such that as you move to shorter wavelengths, the damage threshold decreases (i.e., a LIDT of 1 J/cm2 at 1064 nm scales to 0.7 J/cm2 at 532 nm):
You now have a wavelength-adjusted energy density, which you will use in the following step.
Beam diameter is also important to know when comparing damage thresholds. While the LIDT, when expressed in units of J/cm², scales independently of spot size; large beam sizes are more likely to illuminate a larger number of defects which can lead to greater variances in the LIDT [4]. For data presented here, a <1 mm beam size was used to measure the LIDT. For beams sizes greater than 5 mm, the LIDT (J/cm2) will not scale independently of beam diameter due to the larger size beam exposing more defects.
The pulse length must now be compensated for. The longer the pulse duration, the more energy the optic can handle. For pulse widths between 1 - 100 ns, an approximation is as follows:
Use this formula to calculate the Adjusted LIDT for an optic based on your pulse length. If your maximum energy density is less than this adjusted LIDT maximum energy density, then the optic should be suitable for your application. Keep in mind that this calculation is only used for pulses between 10-9 s and 10-7 s. For pulses between 10-7 s and 10-4 s, the CW LIDT must also be checked before deeming the optic appropriate for your application.
Please note that we have a buffer built in between the specified damage thresholds online and the tests which we have done, which accommodates variation between batches. Upon request, we can provide individual test information and a testing certificate. Contact Tech Support for more information.
[1] R. M. Wood, Optics and Laser Tech. 29, 517 (1998).
[2] Roger M. Wood, Laser-Induced Damage of Optical Materials (Institute of Physics Publishing, Philadelphia, PA, 2003).
[3] C. W. Carr et al., Phys. Rev. Lett. 91, 127402 (2003).
[4] N. Bloembergen, Appl. Opt. 12, 661 (1973).
In order to illustrate the process of determining whether a given laser system will damage an optic, a number of example calculations of laser induced damage threshold are given below. For assistance with performing similar calculations, we provide a spreadsheet calculator that can be downloaded by clicking the LIDT Calculator button. To use the calculator, enter the specified LIDT value of the optic under consideration and the relevant parameters of your laser system in the green boxes. The spreadsheet will then calculate a linear power density for CW and pulsed systems, as well as an energy density value for pulsed systems. These values are used to calculate adjusted, scaled LIDT values for the optics based on accepted scaling laws. This calculator assumes a Gaussian beam profile, so a correction factor must be introduced for other beam shapes (uniform, etc.). The LIDT scaling laws are determined from empirical relationships; their accuracy is not guaranteed. Remember that absorption by optics or coatings can significantly reduce LIDT in some spectral regions. These LIDT values are not valid for ultrashort pulses less than one nanosecond in duration.
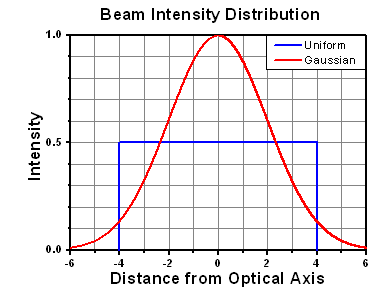
Figure 71A A Gaussian beam profile has about twice the maximum intensity of a uniform beam profile.
CW Laser Example
Suppose that a CW laser system at 1319 nm produces a 0.5 W Gaussian beam that has a 1/e2 diameter of 10 mm. A naive calculation of the average linear power density of this beam would yield a value of 0.5 W/cm, given by the total power divided by the beam diameter:
However, the maximum power density of a Gaussian beam is about twice the maximum power density of a uniform beam, as shown in Figure 71A. Therefore, a more accurate determination of the maximum linear power density of the system is 1 W/cm.
An AC127-030-C achromatic doublet lens has a specified CW LIDT of 350 W/cm, as tested at 1550 nm. CW damage threshold values typically scale directly with the wavelength of the laser source, so this yields an adjusted LIDT value:
The adjusted LIDT value of 350 W/cm x (1319 nm / 1550 nm) = 298 W/cm is significantly higher than the calculated maximum linear power density of the laser system, so it would be safe to use this doublet lens for this application.
Pulsed Nanosecond Laser Example: Scaling for Different Pulse Durations
Suppose that a pulsed Nd:YAG laser system is frequency tripled to produce a 10 Hz output, consisting of 2 ns output pulses at 355 nm, each with 1 J of energy, in a Gaussian beam with a 1.9 cm beam diameter (1/e2). The average energy density of each pulse is found by dividing the pulse energy by the beam area:
As described above, the maximum energy density of a Gaussian beam is about twice the average energy density. So, the maximum energy density of this beam is ~0.7 J/cm2.
The energy density of the beam can be compared to the LIDT values of 1 J/cm2 and 3.5 J/cm2 for a BB1-E01 broadband dielectric mirror and an NB1-K08 Nd:YAG laser line mirror, respectively. Both of these LIDT values, while measured at 355 nm, were determined with a 10 ns pulsed laser at 10 Hz. Therefore, an adjustment must be applied for the shorter pulse duration of the system under consideration. As described on the previous tab, LIDT values in the nanosecond pulse regime scale with the square root of the laser pulse duration:
This adjustment factor results in LIDT values of 0.45 J/cm2 for the BB1-E01 broadband mirror and 1.6 J/cm2 for the Nd:YAG laser line mirror, which are to be compared with the 0.7 J/cm2 maximum energy density of the beam. While the broadband mirror would likely be damaged by the laser, the more specialized laser line mirror is appropriate for use with this system.
Pulsed Nanosecond Laser Example: Scaling for Different Wavelengths
Suppose that a pulsed laser system emits 10 ns pulses at 2.5 Hz, each with 100 mJ of energy at 1064 nm in a 16 mm diameter beam (1/e2) that must be attenuated with a neutral density filter. For a Gaussian output, these specifications result in a maximum energy density of 0.1 J/cm2. The damage threshold of an NDUV10A Ø25 mm, OD 1.0, reflective neutral density filter is 0.05 J/cm2 for 10 ns pulses at 355 nm, while the damage threshold of the similar NE10A absorptive filter is 10 J/cm2 for 10 ns pulses at 532 nm. As described on the previous tab, the LIDT value of an optic scales with the square root of the wavelength in the nanosecond pulse regime:
This scaling gives adjusted LIDT values of 0.08 J/cm2 for the reflective filter and 14 J/cm2 for the absorptive filter. In this case, the absorptive filter is the best choice in order to avoid optical damage.
Pulsed Microsecond Laser Example
Consider a laser system that produces 1 µs pulses, each containing 150 µJ of energy at a repetition rate of 50 kHz, resulting in a relatively high duty cycle of 5%. This system falls somewhere between the regimes of CW and pulsed laser induced damage, and could potentially damage an optic by mechanisms associated with either regime. As a result, both CW and pulsed LIDT values must be compared to the properties of the laser system to ensure safe operation.
If this relatively long-pulse laser emits a Gaussian 12.7 mm diameter beam (1/e2) at 980 nm, then the resulting output has a linear power density of 5.9 W/cm and an energy density of 1.2 x 10-4 J/cm2 per pulse. This can be compared to the LIDT values for a WPQ10E-980 polymer zero-order quarter-wave plate, which are 5 W/cm for CW radiation at 810 nm and 5 J/cm2 for a 10 ns pulse at 810 nm. As before, the CW LIDT of the optic scales linearly with the laser wavelength, resulting in an adjusted CW value of 6 W/cm at 980 nm. On the other hand, the pulsed LIDT scales with the square root of the laser wavelength and the square root of the pulse duration, resulting in an adjusted value of 55 J/cm2 for a 1 µs pulse at 980 nm. The pulsed LIDT of the optic is significantly greater than the energy density of the laser pulse, so individual pulses will not damage the wave plate. However, the large average linear power density of the laser system may cause thermal damage to the optic, much like a high-power CW beam.
Posted Comments: | |
Chaman Gupta
 (posted 2022-07-02 02:12:19.883) Do you have any cage-compatible continuously variable absorptive ND filter wheel? jdelia
 (posted 2022-07-06 12:38:56.0) Thank you for contacting Thorlabs. Unfortunately, our variable ND filter wheels are all reflective. I have contacted you directly regarding alternative options for your application. wiebke.jahr
 (posted 2017-11-22 14:37:42.71) What are the damage thresholds for the ND filterwheel? Can I just use the damage thresholds from the Reflective ND filters (NDxxx series) to estimate? nbayconich
 (posted 2017-12-14 04:11:23.0) Thank you for contacting Thorlabs. The variable filters used in these filter wheels are the same as NDC series UVFS variable filters located here.
https://www.thorlabs.com/newgrouppage9.cfm?objectgroup_id=1393&pn=NDC-100C-2#1389
The damage thresholds recorded on this webpage will be applicable for the NDM series filter wheels. user
 (posted 2017-10-31 17:17:53.163) What intensity can this handle? Thanks. nbayconich
 (posted 2017-12-27 04:47:37.0) Thank you for contacting Thorlabs. The variable filters used in these filter wheels are the same as NDC series UVFS variable filters located here.
https://www.thorlabs.com/newgrouppage9.cfm?objectgroup_id=1393&pn=NDC-100C-2#1389
The pulsed damage thresholds recorded on this webpage will be applicable for the NDM series filter wheels. We do not yet have CW damage threshold data for these optics. Please reach out to us at techsupport@thorlabs.com to discuss you application for these filters. Benjamin.krueger-extern
 (posted 2017-01-11 12:56:05.58) Hello,
How is the spectral Transmission up to 1600 nm? Is there any data available? We would like to measure at 1550 nm with your Filter wheel tfrisch
 (posted 2017-01-20 09:44:14.0) Hello, thank you for contacting Thorlabs. For most NIR applications, the Inconel coating would still have a suitable reflectance, but I will reach out to you directly to discuss your application. patrick.lu
 (posted 2015-08-03 18:00:38.63) Is there a way to replace the continuously variable filter with one that has discrete steps? We would like to use something like this in a camera imaging application, but we don't want one side of the field of view to experience different attenuation from the other side. besembeson
 (posted 2015-08-19 02:11:33.0) Response from Bweh at Thorlabs USA: I will followup with you on a special quotation and discuss your application further. Michael.Roth
 (posted 2013-10-21 17:25:01.78) How does the reflective ND-filter work when light travels in the wrong direction through the filter?
In my application the ND-filter would stand in front of a mirror, so the light would travel through the filter in both directions.
Thank you for your help. tcohen
 (posted 2013-10-29 13:14:00.0) Response from Tim at Thorlabs: The ND filter can be used in reverse. Only one side is coated, so instead of having your first surface with an attenuation to reach a specified OD and having a Fresnel reflection on the back surface as a percentage of the remaining power, you will instead have the Fresnel reflection as a percentage of the original incident power. So you change the ratio of the reflections of the two surfaces. user
 (posted 2010-08-24 17:53:39.0) A reply from Jens at Thorlabs: this product is based on a continuously variable metallic ND filter and hence is reflective. rjaculbia
 (posted 2010-08-24 05:21:13.0) is the nd filter wheel here reflective? Thanks. |